Emily Swan has been Electrical Design Engineer at Radial for over 4 years, we wanted to chat with her about her career path as a pro audio engineer, the nature of working in a male-dominated industry, as well as some insights into the design of the new Reamp® Station.
Here is the full interview.
Radial: Share a bit about your background. What influenced you to choose pro audio and engineering as a career path?
Emily: Electrical engineering and pro audio merges my two passions — designing technology and a love of music. Growing up, I gravitated to science and math courses as equally as I gravitated to concert, band, choir courses.
Radial: Talk a little about your formal schooling.
Emily: In my first years of university, I pursued a degree in electrical engineering. At that time, I felt a major disconnect between what I was learning and what I wanted to do for my career. I felt the same disconnect too when I started pursuing co-op jobs, which are very similar to engineering internships in the States. You get to try out an industry and career while you’re still in school to see if it’s the right fit.
Radial: It sounds like something just wasn’t clicking for you at that time.
Emily: Yes, I think it was a combination of having a lack of purpose combined with the lack of creativity that exists in most electrical engineering jobs. And so going into my third year of university, I ended up adding the music option to my electrical engineering degree with an emphasis on audio signal processing and recording techniques. Also at this time, I joined two community choirs and instantly felt a calling back to my true self.
Radial: Talk a little bit more about that experience.
Emily: Through my choral director, I was able to volunteer as an open mic technician and this really solidified my love of working with audio gear. And it really correlated to what I was learning in school to learning about audio signal processing and recording. Upon graduation, I found it was quite difficult to find a job in the music industry in Canada, and in particular on the West Coast in Vancouver.
Radial: What did you do once you set out looking for a job?
Emily: After I graduated, I ended up pursuing a company I had worked for as a co-op student. But after a couple of years, I realized it really wasn’t the right fit. I ended up taking a gamble and applying for a senior engineering position at Radial when I was still very much a junior engineer in terms of my experience level. But luckily, Radial was also looking for a junior engineer as well so they gave me a callback and the rest is kind of history. I’ve been working at Radial and working in audio ever since.
Radial: So you had a background in music and mixed it with a love for engineering. Did it feel like a natural step to mix those two together?
Emily: Yes, from the beginning. And honestly, when I went to university, I had no idea that there was this opportunity to work in music. I kind of just discovered it. I really liked electrical engineering, but I didn’t know I could blend those two passions until my third year. Then of course, when I graduated, it was kind of like, “How can you find a career with this very particular skill set?” So I kind of lucked out too when I found Radial.
Radial: What was it that drew you to Radial?
Emily: I had heard of Radial when I was working as a sound tech. We had a couple DI’s on stage, but I had no idea the company was based in Port Coquitlam until I saw the job posting and I was like, “Hey, Radial, I recognize this company.” And I read the description of the senior engineer and I was like, “Wow, this is my dream job.” This is something that I would really like to do one day. I knew that I probably had a handful of the skills that were on the list of requirements, but I still put my name out there anyways.
Radial: So you were at the right place at the right time?
Emily: Yes, there was a bit of fate and I wasn’t happy with my job at the time, so I was checking job boards and trying to get a feel for what else was out there. And since I wasn’t loving the pure engineering industry, I was also looking at sound technician jobs and exploring that direction. So I kind of lucked out in both regards finding an engineering job and finding something that was in audio.
Radial: Talk about some of the challenges you face being a woman in the primary male-dominated field of engineering.
Emily: Definitely when I was fresh out of school as a female junior engineer, I felt I had to prove more and justify my role more than my male colleagues. During meetings, I was often asked if mine was a non-technical position or if I was an administrator for the engineering department. This was before I joined Radial, of course.
Radial: That must have been awkward!
Emily: Yes it was! And this was when I was meeting with clients, distributors, different departments. And the more I was questioned about my position and being in that position, I began to question more why I was in the field. It was hard having to justify to myself every day as to why I was there. And there were many times that I did want to leave engineering. Like I mentioned, I was actually exploring maybe becoming a sound technician and going back into music just because I was really struggling with being in an engineering department and the people and the conflicts that I encountered on the job almost every day.
Radial: And this was about the time you found the posting for the position at Radial?
Emily: Yes, I was very fortunate to discover Radial. My exposure to pro audio has mostly been through Radial. Even though I work predominantly with male colleagues in the Radial engineering department right now, I have never felt unseen or undervalued like I did when I first graduated from school.
Radial: Did you still feel you had to prove yourself?
Emily: Yes, I did have to prove myself to obtain solo design projects, but that is very much the same for any new engineer. And I mostly remember that I am a woman in a male-dominated field when I am meeting folks from the industry outside of Radial. So mostly if I’m going to tech conferences or meeting with distributors, I often still have to explain my position. And I do still find that when I explain my position, many are surprised to learn that I’m a professional engineer and that I have over seven years of work experience.
Radial: Do you get the sense that the trend of women working in pro audio engineering is changing?
Emily: I think it’s still not the normal career choice for a woman. So there’s still a surprise element. But definitely, the advantage I see to being a woman in engineering is that my role does help pave the way for this industry to become more inclusive. I can create a safe space for young women engineers to build their careers. We’ve already had a couple of young engineering co-op students in the department and it is a great opportunity to be able to mentor and to give back.
Radial: Do you see yourself as breaking the stereotype of a typical engineer?
Emily: I do pride myself as being an approachable person. I do not know if that’s more a personality trait versus being a woman, but nevertheless, I think I am often seen as someone at Radial within the engineering department where people feel safe asking questions and seeking advice from. If you think of the stereotypical electrical engineering professional, you might think of someone who is a little bit more introverted and standoffish. So, I think it’s great when you have different personality traits in the department and different people. So I think being a woman kind of brings that perspective into our department.
Radial: Do you see the role of the engineer transitioning and morphing as a general trend?
Emily: I think it’s great when engineering departments can diversify because I find we can kind of help each other out with our strengths and weaknesses. And we do have some employees in our department that are a little bit more introverted or just don’t want to have a very close relationship with production. They would rather focus on their designs, focus on their projects. And both of those roles are valid, but you do need people in there that can integrate and communicate cross-department.
Radial: Does this trend towards diversity go beyond engineering?
Emily: Yes, I think engineering isn’t the only industry that realizes it needs to change. I think this field is more vocal about it because women are still such a minority in this field, so I feel like that’s why it’s a conversation.
Radial: Let’s talk a little bit about the products. Using the new Reamp® Station as an example, what’s the first thing you do when you start on a new project? Where do you put your focus?
Emily: I usually start by analyzing the whole system. When I get a new project, I usually look at everything as a whole, and then I’ll start breaking down the system into smaller components. When I get it to components that I’m happy with, I start researching and designing and building those individual components one at a time.
Radial: So you take it stage by stage?
Emily: Yes, as I build one stage, I will start to build upon it, such as building the second stage. For example, with the Reamp® Station, I started with the input stage and then kind of looked at how that was sounding; what I was emphasizing, and then looking at what components I should use for the output stage. So we had something that was comprehensive and consistent throughout the design.
Radial: You mentioned that you start kind of by breaking down the stages. Are you talking about the stages of the circuit flow of the product itself, like from the input to the inner workings, to the output?
Emily: Yes, exactly. So I look at the desired feature set that the tech team wants us to include in the product. I look at the signal flow from input/output and kind of look at where we can start including those blocks. And then once we have a good block diagram and a good flow, it’s down to choosing what we want to do in each section.
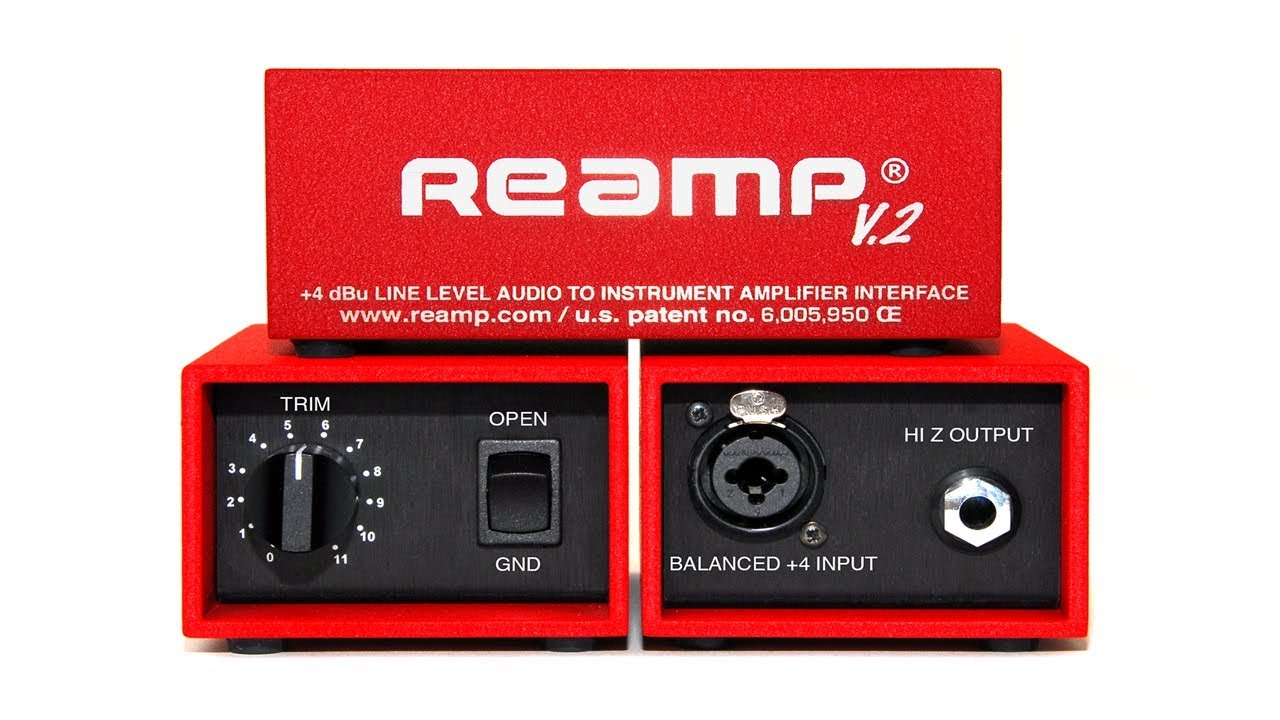
Radial: Some people may be familiar with John Cuniberti, who built the first reamper back in the 80s. Radial acquired John’s company and began manufacturing the JCR based on his original design. John mentioned in this interview that the original idea for his Reamp® box was a combination DI and reamper, similar to what the Reamp® Station is today. Were you aware of that?
Emily: No, I wasn’t! That’s really cool to think that the new Reamp® Station has evolved in a way to circle back to the original intentions that John had when he started out!
Radial: Talk a little bit about the influence that John’s design had on your process of designing the Reamp® Station.
Emily: I was introduced to John’s original reamper and was able to take a look at it, explore the design a bit. We had talked about using the JCR circuit early on and it was nice to be able to take a look at the original box and confirm that using that circuit design would be the right thing for this box as well.
Radial: Did you consider any other DIs along with the JCR?
Emily: Yes, I also looked at the ProRMP which is a great device, but just thought that the transformer in the JCR would be a better fit for the design intentions of the Reamp® Station. The JCR essentially has a patented Reamp® transformer in it which is what makes it so special. I knew it would be a slam dunk to put that circuit in the Reamp® Station.
Radial: Did the JCR’s passive design have any influence on your decision?
Emily: Yes, definitely. The fact that the JCR is a passive device helped make both sides of the Reamp® Station — the DI side and the Reamp side® — have more isolation between the two. This allowed me to do a lot with the circuit board to make sure that the two parts were completely separate from one another.
Radial: Did you have some experience with the JCR before?
Emily: Yes, a couple of years ago I worked with the engineers on the Reamp® JCR so I did have some insight into the unit and the circuitry. By the time we finished that product, I had a pretty good familiarity with the JCR itself. John’s association with the JCR is of course legendary, and it was a real honor to sort of follow in his footsteps in expanding the design with the Reamp® Station.
Radial: Talk about some of the challenges and some of the highlights with regards to the Reamp® Station, from an engineering perspective.
Emily: For the Reamp® station, probably the trickiest part was the power supply. It’s really low current. Since it’s a phantom power device, the goal was to try and build a good DI that doesn’t generate a lot of current while still being very clean and having a very clean signal path with good isolation. So that took quite a bit of work and fiddling around with. And you don’t get to choose what power supply you’re using for phantom, it’s always an external source. So the goal was having enough filtering so that, like I mentioned earlier, we have enough isolation. And it was also playing around with audio op amps or doing the output drive stage for the DI, something that had low power consumption, but still sounded good and still was going to work nicely in the design.
Radial: Sounds like you spent quite a bit of time and effort getting this stage right.
Emily: Yes, there definitely was a lot of playing around with that. Just a little recap on what a DI does … it takes in an unbalanced high impedance instrument signal and then converts it to a balanced DI output. So the goal is trying to keep the impedance high even when you have a through jack that goes to a guitar amp.
Radial: How did some of the existing design criteria come into play in this design stage?
Emily: With some of our older products like the J48, it’s tricky to not have your instrument be loaded down by the guitar amp when you have it through. So the goal with the Reamp® Station design was just looking at clever ways to use a switching jack. We actually implemented a buffer stage as well, but were able to introduce some cool new features from listening to feedback from different customers.
Radial: What’s unique about the Reamp® station versus some of the other Radial DI boxes?
Emily: I used a brand new really nice op amp for the Reamp® Station. And it’s definitely a new op amp to the Radial line. So whenever you use a different op amp, it brings out a new sound and color. This one is definitely meant to be low noise, low distortion. It still has the driving capabilities for DI, but definitely an improvement in that regard. And as I mentioned earlier, most of our DIs don’t have this input buffer as well for a guitar amplifier through. So that’s a new added feature with the Reamp Station, which improves the integrity of the signal going through to the output stage, but then it also improves the signal integrity. That’s going to your guitar amplifier as well. So overall a really great improvement of the design.
Radial: For those that may not know, describe what an op amp is.
Emily: The op amp is called an operational amplifier. And it’s a component that could be configured as an amplifier, or it could be configured as a buffer, so it helps convert impedances. So for the Reamp® Station, since it is a new amplifying device, it is configured more to drive the output signal. So it can change the color of your sound because it’s not a complete passive signal. So any electronics that you put in a signal path can add some color, distortion, and any of those factors of noise, but depending on the amplifier used, the op amp that you choose and how you use it, you can achieve the cleanest sound possible. And in a DI application, that’s really what you’re trying to achieve. You’re trying to really capture that signal integrity of the instrument.
Radial: And when you say capture the signal integrity, does that mean keep it as pure and true to the original as possible?
Emily: Yes, it is basically to keep the integrity of the original input, not build and improve upon it. And it’s basically so you can have an output device like a source device such as mixer or a dub where you’re able to record that instrument and still have the integrity of the signal.
Radial: Talk for a second about the lessons you learn along the way when designing a new product like the Reamp® Station.
Emily: I find that you learn a ton when you complete any new project from start to finish. Even though the Reamp® station may have been smaller compared to my last project, the PZ-Pro, I do find it builds upon my knowledge of audio components. It gives me the opportunity to work really closely with Hutch (Radial’s senior design engineer) and to kind of get his insight on audio principles and testing techniques, and also kind of dip into his extensive knowledge of audio components and what he looks for in his designs and kind of shape how I can apply that to my own.
Radial: So there’s a continuum of learning along the way.
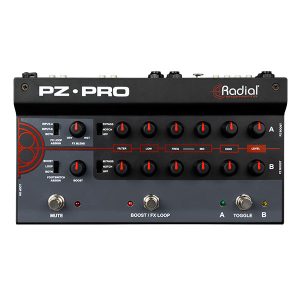
Emily: Yes, it’s great kind of going through the full process from start to finish. You learn a lot. And there’s also this whole element of which I’ve been kind of dealing with for the last six months, which is designing for production since the Reamp® station is going to be a product that goes through larger production runs.
Radial: You mentioned the PZ-Pro, another Radial product you designed. Was the approach to designing the PZ-Pro similar to the Reamp® Station as far as from a philosophical standpoint?
Emily: Yes, I did follow a very similar path. But talking about earlier how you have a really big system with a really large feature set, which is what the PZ-Pro is in a nutshell, it really benefited from breaking down the design process into those smaller components. And the amount of research and development that I did into the EQ of the PZ-Pro was just so rewarding. Also, just building all those circuits on a breadboard, listening to them one by one and making little tweaks and then finally getting to the point where I could put everything on its own circuit board. That was rewarding. And designing the PZ-Pro for manufacturing was also extremely difficult as well, since it implements two daughter boards and a main board.
Radial: So while the two are very different products, the PZ-Pro and the Reamp® Station, the design process was similar.
Emily: Yes, it was great to go from start to finish with the PZ-Pro and then take on a smaller project like the Reamp® station, which still had its problems that it had to solve. But it was great to be able to do something so large and then kind of scale it back and implement those same processes on the Reamp® station.
Radial: Let’s switch gears a bit and talk about what advice you’d have for other women engineers who may be considering a career in pro audio. What advice would you have for them?
Emily: I would definitely tell them that the pros outweigh the cons if you love doing what you do. It is okay to admit that it is difficult to work in male-dominated spaces. I definitely wish I had given myself more grace versus I often would blame myself for other people’s ignorance if that makes sense. But I don’t think women engineers, I don’t think they need to change to become thicker skinned.
Radial: What’s one change you would like to see happen sooner than later?
Emily: I definitely believe the system as a whole needs to just become more inclusive. And the other thing is I’ve met some wonderful people in the industry and I’m really glad I stuck it out. Not everyone you meet is a bad apple, I guess, is the other way to phrase it. Definitely, the people that I work with now here at Radial and just how inclusive the environment … it definitely restores my faith in the industry-changing and how it’s supposed to look. So it’d be great to kind of emphasize that and to tell young women engineers that it does get better and we’re trying to make it better too.
Radial: What about someone that may not have that advantage of being in a city that’s a center of the industry, like Vancouver? What can they do if they are not located in a major city?
Emily: I do think engineering as a whole is changing due to COVID. I do think there’s more remote jobs out there. So definitely not being in the hub isn’t too much as a factor as it used to be. For example, right now, I’m working out of Sioux Island and I go into Radial home office in Port Coquitlam, in the Vancouver area, once a month to kind of catch up and follow up with production on my projects and stuff like that.
Radial: So engineering jobs are becoming less city-specific?
Emily: Yes, I think that hurdle is changing. As for meeting people and getting exposed to the industry, I would really recommend a student engineer go out of his/her comfort zone by moving to new places and trying to build a career in audio if possible. And if that’s difficult, reach out through the different engineering groups either on campus. Just reaching out to people and trying to engage and build mentorships.
Radial: What trends do you see on the horizon that you think are going to influence the design and production of pro audio gear in the coming years?
Emily: This is a tricky question to answer, and I can really only answer it from an engineering perspective. But definitely what I’m battling as an engineer post-COVID is just the influence that COVID had on the supply chain and what that has done to the design world. It has definitely made engineering more difficult. It adds a lot more constraints for product development because I find you have to kind of adapt your design processes to fit the state of the supply chain environment. This systematic approach that I was talking about earlier, even though you may not have everything figured out for the design, you have to point out very early on what components are going to be difficult to source and start thinking about it very far in advance because most components are a 56 week lead time. So if you want to do a production run in the next year, you have to really be thinking ahead.
Radial: What improvements has Radial made to adjust during these challenges?
Emily: We’ve improved our testing software to ensure the best results from new components. There are more open source and different audio analyzers out there. We actually use them in production to make sure that the quality of our products are being captured there, that we’re making sure things that are going to customers are at the appropriate level and stuff like that and not having to use a really fancy piece of the kit to do that. And we’re also automating that process too so there’s less human intervention like inserting cables and pulling out cables to complete tests. We’re able to just have all that switching done automatically. And then as Hutch always loves to remind me we’ve upgraded our labs and what testing capabilities that we can do and we’re really lucky.
Radial: How has working with Hutch [read an interview with Hutch here] changed your perspective on engineering and design?
Emily: I’m really fortunate that I get to work with someone like Hutch who has worked at some amazing companies in the past and just get his insight into what he checks when he is testing. And so that really helps as well and we’re able to pass that down to junior engineers and our co-op students as well, get them excited to work in audio. It’s been a really rewarding experience working with Hutch, and continuing my journey in engineering and design here at Radial.
To read an interview with John Cuniberti, click here.
To read an interview with Hutch, click here.